Quality Control
Italian Textile Biella
40th Anniversary
I.T.B. is synonymous with quality. Since 1980, we have been treating fabrics with the same enthusiasm and passion which, in time, has allowed us to become the acclaimed leader of our sector.
Over the years, and with our accumulated experience, we have found that buying and selling fabrics of the highest quality has resulted in success for us and also for all our clients.
SELECTIONING AND PURCHASE
Our Purchasing network, built up over the years, ensures privileged relationships with our suppliers, which in turn ensures we are able to obtain the best fabrics that will meet the requirements and scrutiny of our clients.
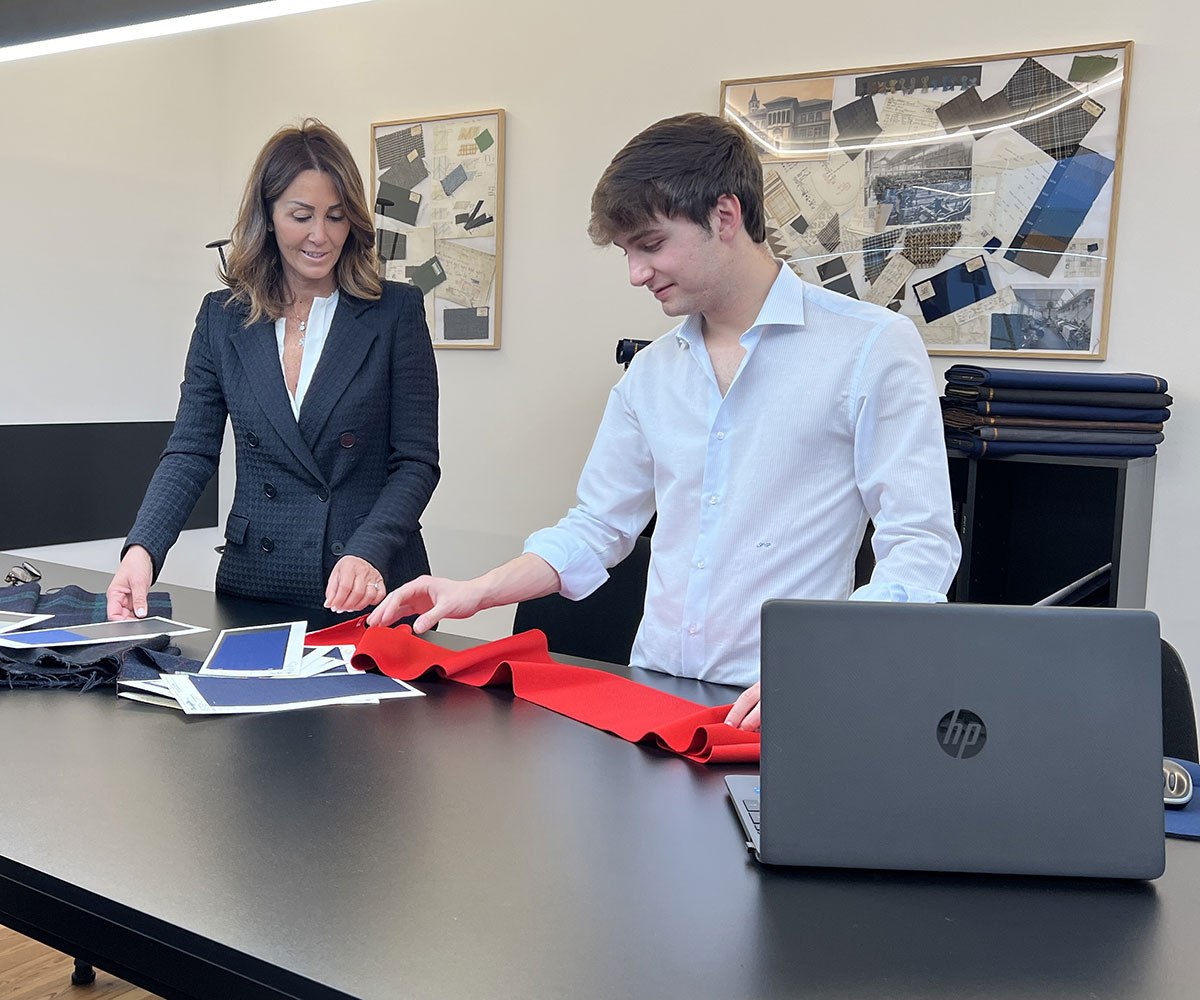

QUALITY CONTROL
Once the products have arrived at the warehouse, our employees carry out all the necessary control checks. They verify the suitability in respect of the quality of the yarns, the accuracy of the colours and the meterage.
Quality is the foundation on which we base our service. In the rare occasion that our products fail to provide total satisfaction,then they can be returned immediately.
All our fabrics are first choice, directly checked by us for quality and length.
SAMPLING
When all the controls have been completed and the quality of the product has been validated, the sampling commences. All the information is recorded to ensure a quick and easy workflow.
Photographs of the samples are also taken using specialist equipment which guarantees the accurate calibration of colour tones, This ensures that the photographs correspond as closely as possible to the original fabric.
Each label of our samples has a QR-CODE, with which you can check the actual availability of the item in real time with the exact length.
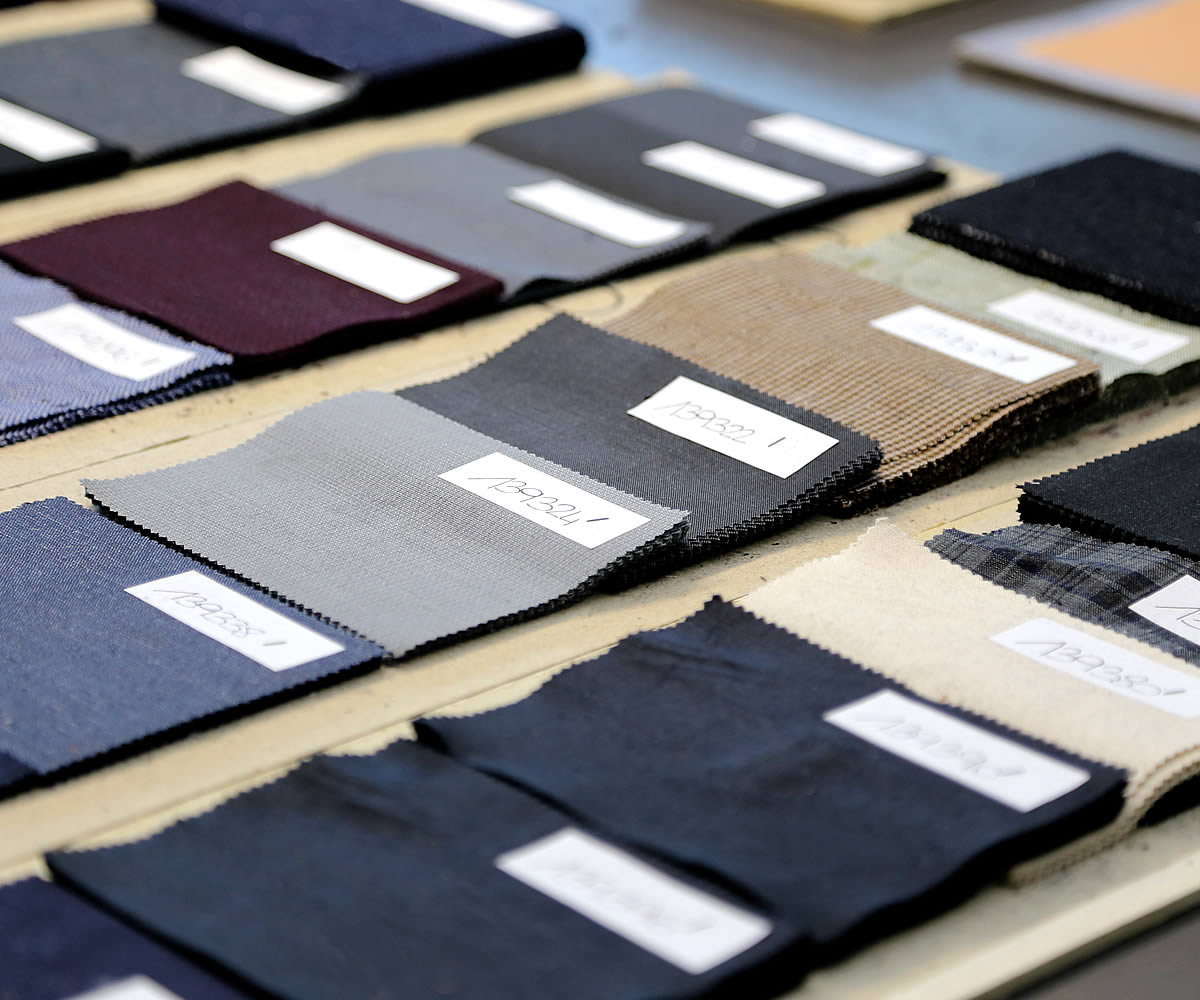
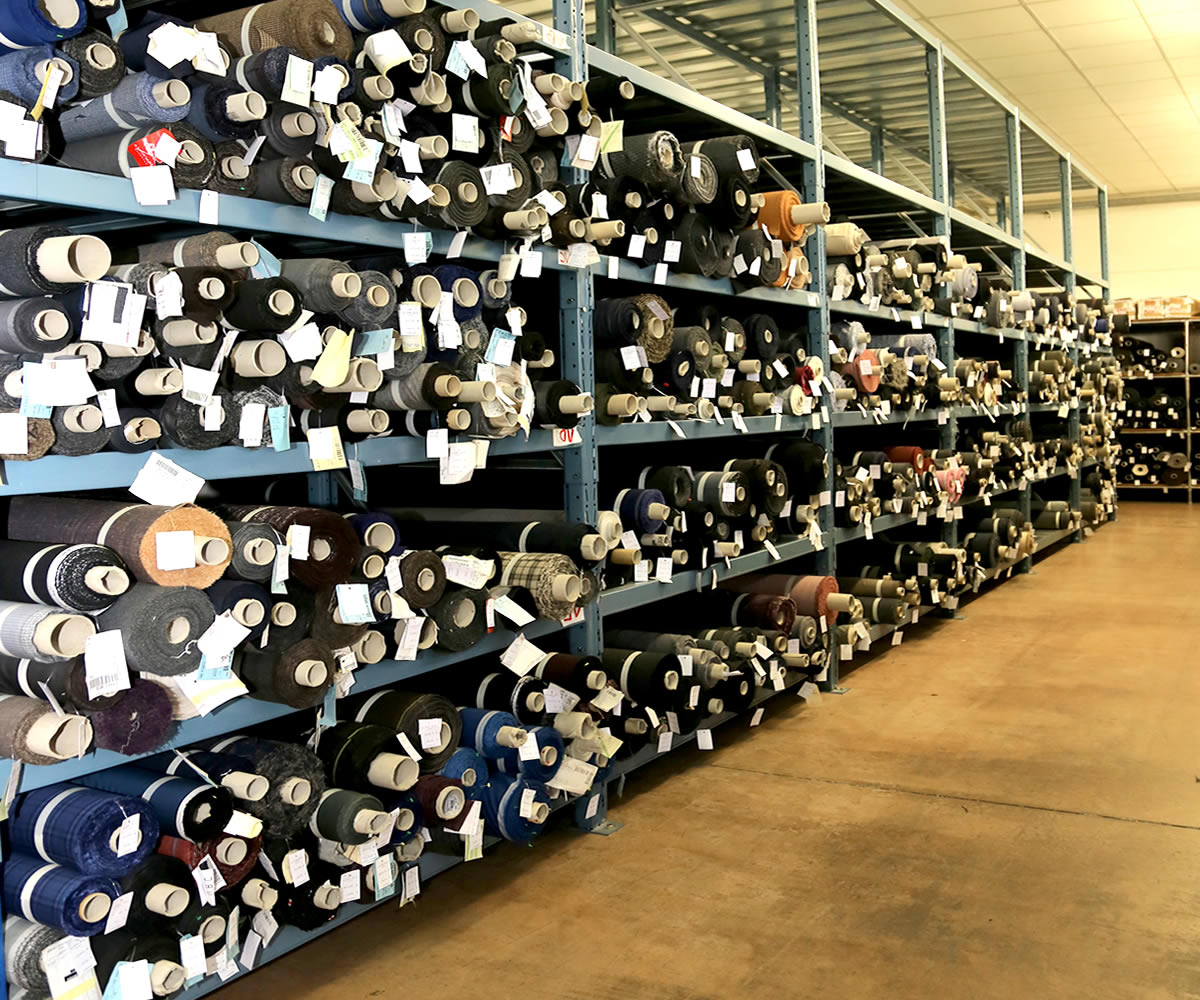
STORAGE IN THE WAREHOUSE
After the sampling the fabrics are painstakingly prepared for storage in the warehouse. The colours of, for example, the fabric and yarns are guaranteed by constant controls of temperature and humidity.
A regular moth treatment (insecticide and repellent) is used in the warehouse to prevent damage thus preserving the quality of the fabrics.
To avoid any errors in the next steps, an automatic patented warehousing system controls the precise storage locations.
AFTER SALES PREPARATION
Once the order is retrieved from the warehouse, we verify the compliance and quality of the fabric to the specific requirements of the buyer.
All appropriate customs documentation will be prepared and if necessary we can provide information about couriers.
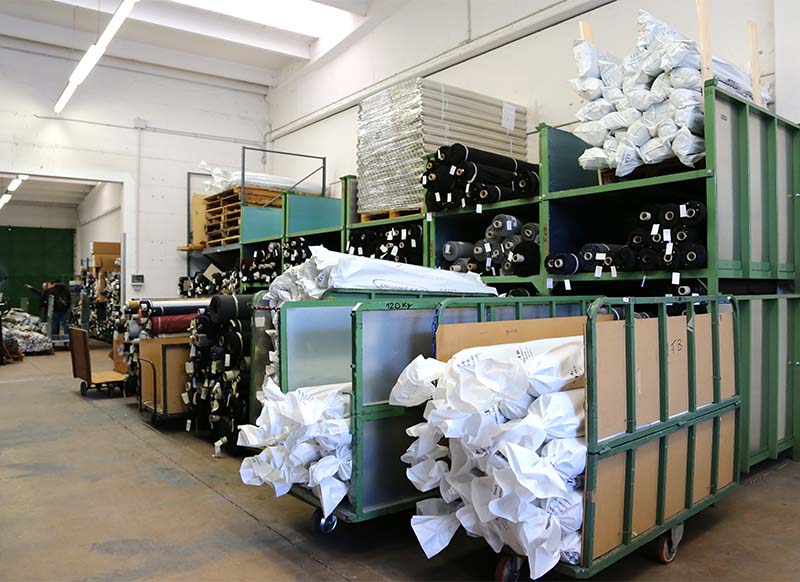
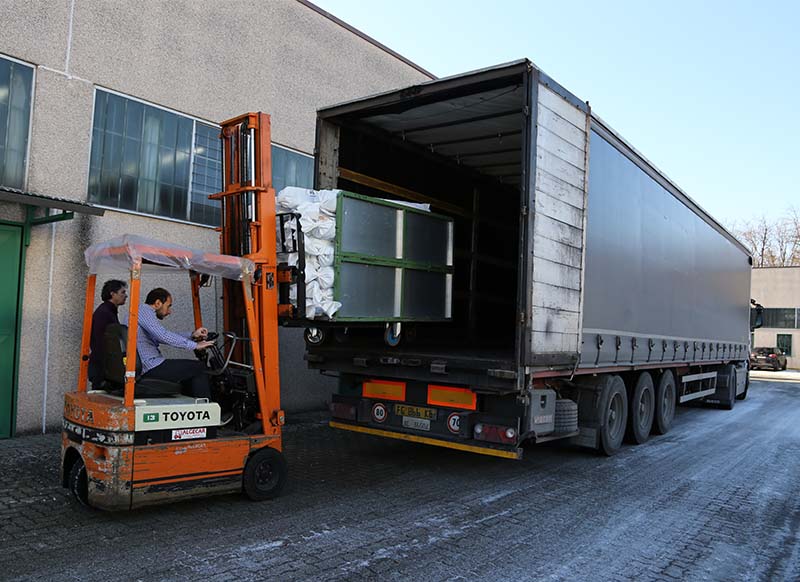
SHIPPING
We also pay particular attention to the preparation for shipping. The fabrics purchased by our clients, are carefully packed so as to avoid any damage during transport. They are all labelled and verified according to conformity and/or compliance of the product codes.
The packaged merchandise is then stocked in a secure area, pending the arrival of the courier service. It is then loaded with all necessary care in order to maintain its quality and integrity.